Taiyo Nippon Sanso Corporation (Headquarters: Shinagawa-ku, Tokyo; President: Kenji Nagata; hereinafter “TNSC”), a Japanese industrial gas company in Nippon Sanso Holdings Group, conducted a demonstration test using the Innova-Jet
® Forehearth oxy-fuel burner for glass manufacturing processes installed at a customer's production facility in Europe. This test was conducted jointly with Nippon Gases Euro-Holding S.L.U. (Head Office: Madrid, Spain; President and Representative Director: Raoul Giudici; hereinafter "NGE"), a European industrial gas company and was verified that the burner reduced the CO
2 emission by 65%.
To reduce CO
2 emissions from many industrial furnaces in Japan and contribute to the realization of a carbon neutral society, we are developing oxygen combustion technology for application in various industrial furnace processes.
News Release PDF
1. Demonstration test results
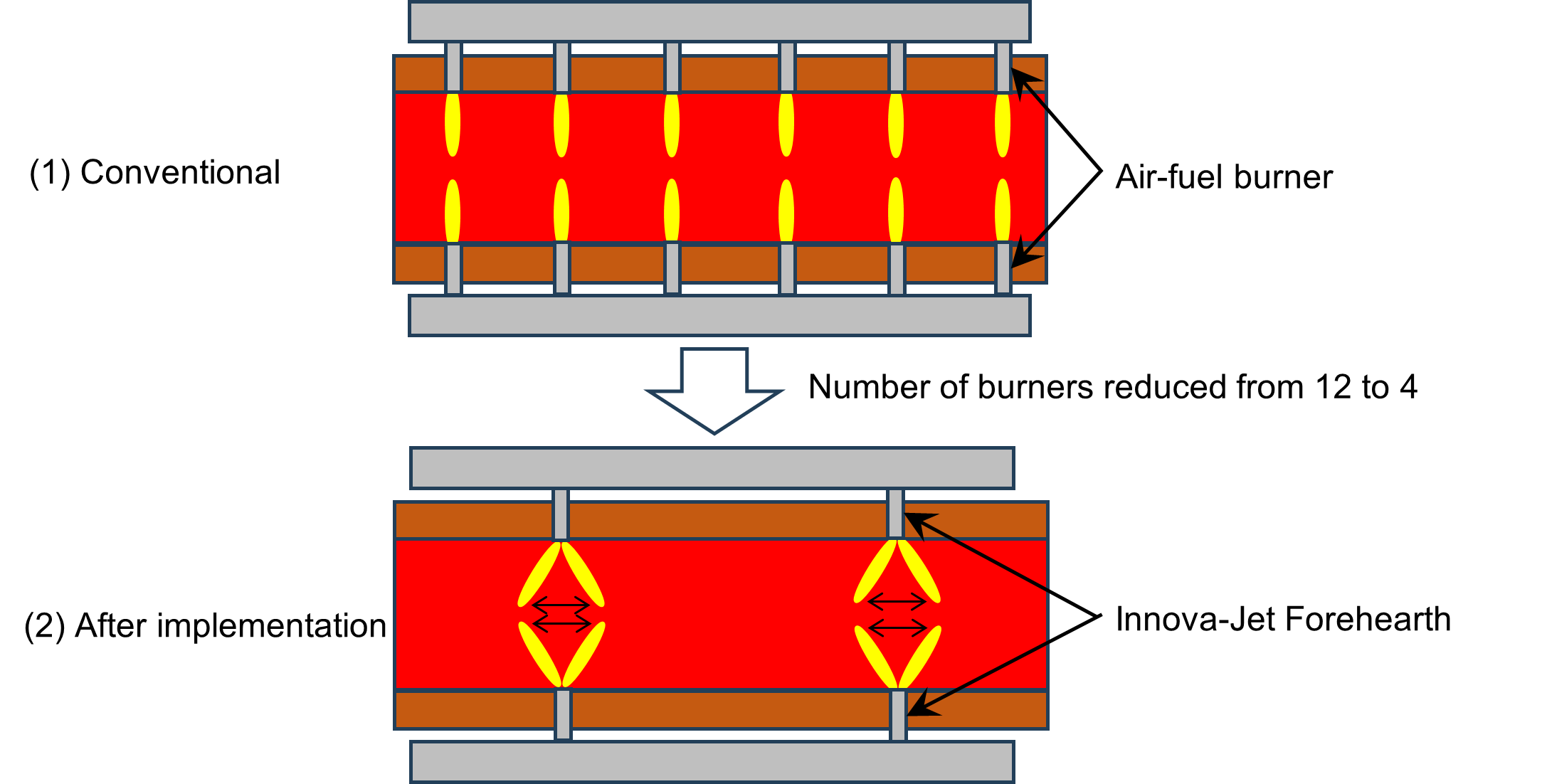
Fig. 1 Comparison of conventional operation and operation with Innova-JetⓇ
Forehearth implementation
Table 1 Demonstration test results
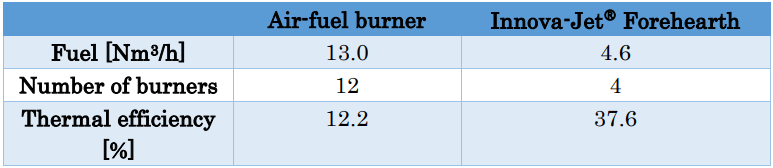
TNSC and NGE installed Innova-JetⓇ Forehearth burners on a forehearth*1 at a customer's plant in Europe to conduct a demonstration test. As a result of replacing 12 conventional air-fuel burners with four Innova-Jet® Forehearth burners, we confirmed that the forehearth could be heated uniformly without any anomalies such as local overheating. It was also verified that fuel consumption could be reduced by 65% compared to conventional operation. In addition, the Innova-JetⓇ Forehearth has proven to provide operational benefits such as less burner maintenance due to the reduced number of burners.
TNSC and NGE will continue to develop oxy-fuel burners that can meet the needs of customers in various industries, including glass manufacturing, to achieve low environmental impact.
*1: The forehearth, which has a long, tunnel-like shape, distributes glass melted in glass melting furnace to molding machines that shape the glass into bottles and fibers. The inside of the forehearth must be maintained at a uniform, high temperature to keep the glass in a molten state.
2. Technology overview
A forehearth, which is responsible for maintaining the temperature of molten glass, consumes between 6% and 45% of the fuel used in the entire glass production process. Since air-fuel burners are usually used in forehearths, the implementation of oxy-fuel burners allows fuel savings. The Innova-JetⓇ Forehearth designed for forehearths was launched in 2018 as part of our oxy-fuel burner lineup.
The Innova-JetⓇ Forehearth uses oxygen combustion technology to significantly improve thermal efficiency. It also utilizes self-oscillation*2 to oscillate the flame, thus achieving uniform heating over a wide area in furnaces with small combustion spaces such as forehearths.
*2: In this technology, self-oscillation or self-induced oscillation, is generated using a fluid flow phenomenon known as the Coanda effect, in which the jet flow from a nozzle tend to stay attached along a nearby surface. By applying this technology to a burner, it is possible to change the direction of the flame periodically
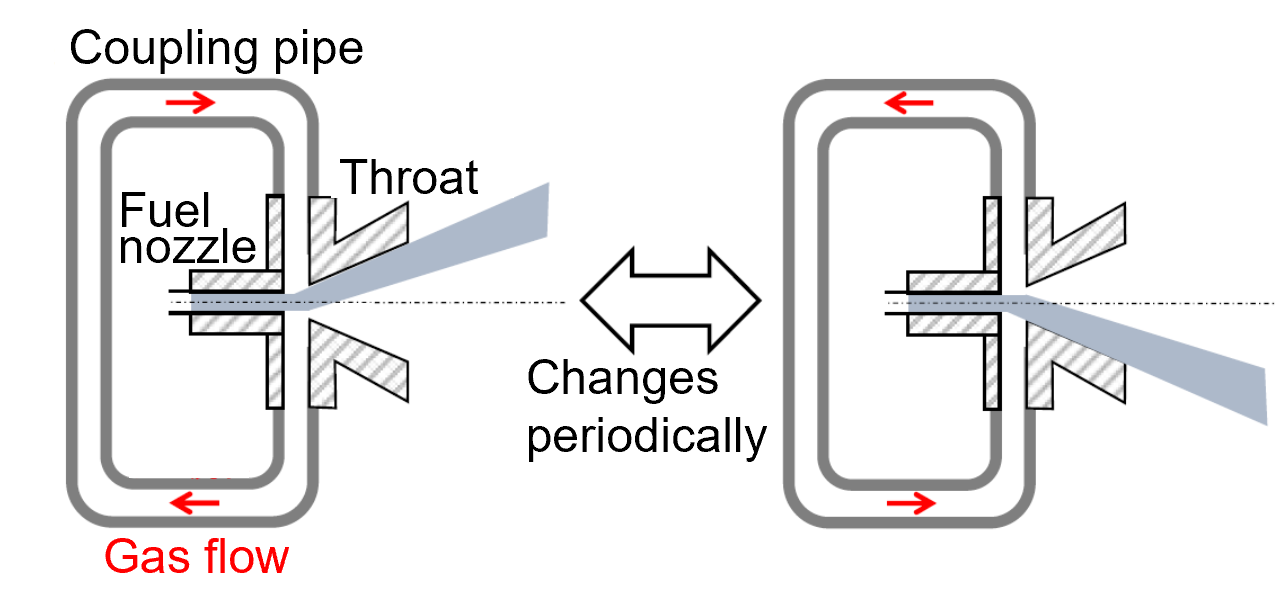
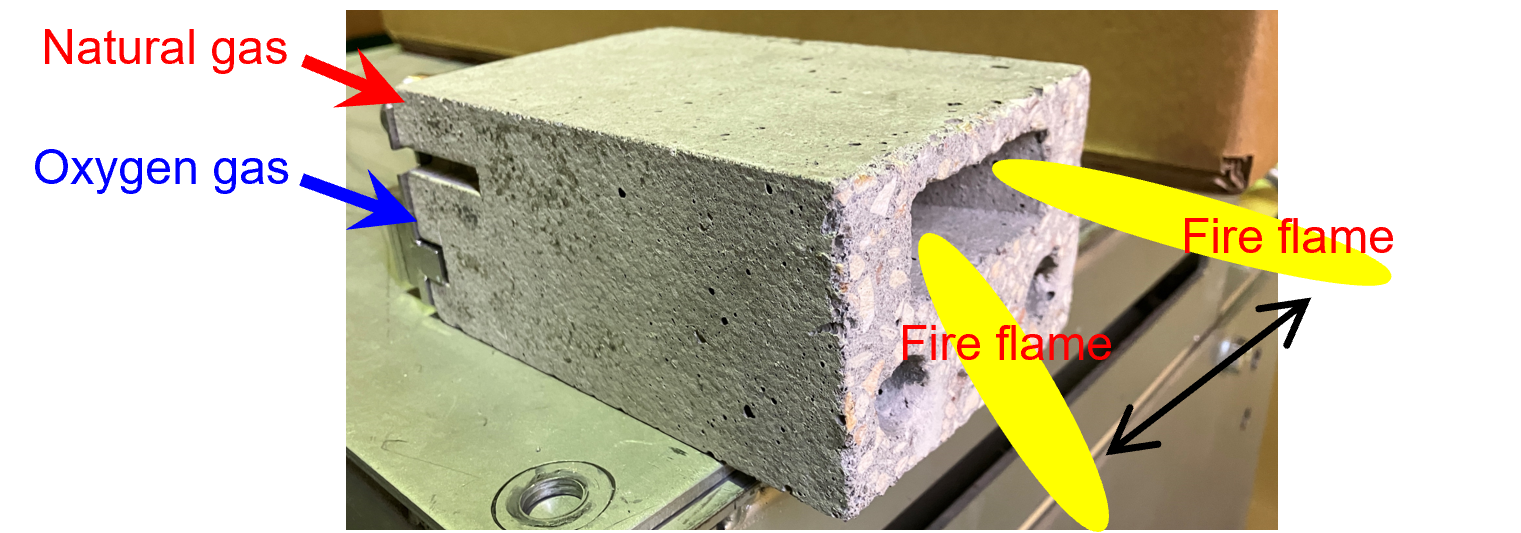
Fig. 2 Principle of self-oscillation (top), and photo of the Innova-JetⓇ Forehearth
(bottom)
Taiyo Nippon Sanso Corporation
Tnsc.Info@tn-sanso.co.jp