Metal 3D printers are increasingly being utilized primarily in Europe, the United States, and China. In Japan, the use of 3D printers is rapidly increasing not only in the aerospace and defense industry but also in a wide range of fields such as the molds and general industry. In the metal 3D printer market, which is expected to experience high growth in Japan in the future, our company has been providing customers with a range of solutions that other companies cannot offer by leveraging our core gas-related technologies and expertise that we have cultivated to date. This time, we interviewed Yusaku Nanao (“Nanao”), Yusuke Yamaguchi (“Yamaguchi”), Yuji Ono (“Ono”), and Subaru Nakanishi (“Nakanishi”) from AM Innovation Center, Innovation Division, Innovation Unit, who are engaged in technology development related to metal 3D printers. They will present our strengths and solutions in the field of metal 3D printers.
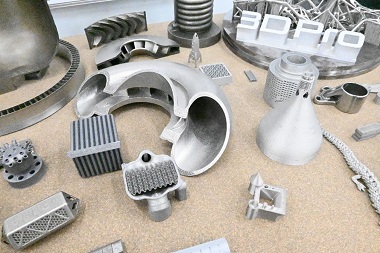
A variety of samples manufactured by world-leading metal 3D printers in AM Innovation Center
Q1:What are the market trends for metal 3D printers in Japan and overseas?
Yamaguchi:I was reminded of this during a recent business trip to the United States, where practical applications are steadily advancing particularly in Europe and the United States. Companies utilizing 3D printers encompass a wide range of industries, including aerospace, medical and automotive, and some even use metal 3D printers for engine manufacturing. Although I feel that the use of 3D printers is spreading rapidly in Japan, I think there is still a lot of room for further expansion compared to the widespread use in the United States and Europe.
Ono:The slower rate of expansion in Japan compared to Europe and the United States may be due to a different way of thinking about risk. In Europe and the United States, encountering technical obstacles is considered a necessary part of the development process. Therefore, even if an unintended development issue is found, it is never considered a “failure.” Conversely, in Japan, there is a strong cultural tendency to perceive it as a failure. Even if switching from the conventional development process to metal 3D printers can lead to increased productivity, functionality, and performance improvement, they may avoid potential new technical issues that may arise during the development process. Recently, however, I have noticed a growing number of customers expressing a willingness to explore new possibilities with 3D printers, without being hindered by the fear of failure.
The challenge lies in the stability of modeling quality
Q2:What are the challenges customers face in using metal 3D printers?
Nanao:Many of our customers inquire about the stability of the quality of objects produced by metal 3D printers. There are various methods of modeling with metal 3D printers, but welding and sintering are common operations used in the solidification process of the modeled object. We frequently receive inquiries from customers who are troubled by issues related to the inconsistent quality of the modeled objects, stemming from variable factors such as material properties, seasonal changes, and environmental conditions.
Nakanishi:This issue is often attributed to moisture in the material and humidity in the modeling environment. Moisture in the metal powder used as the material can disrupt the modeling process, resulting in problems such as the design not being completed as intended. The modeling environment is also important. During modeling, the local shield and modeling chamber are filled with argon gas or nitrogen, but our research has shown that fluctuations in the amount of residual oxygen and moisture can cause instability in the quality of modeled parts. The approach of stabilizing the modeling atmosphere is exactly the solution we have been providing to our customers for many years through gas technology.
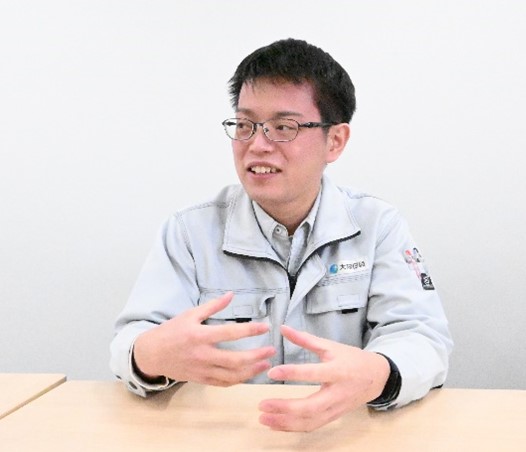
Mr. Nanao (left) and Mr. Nakanishi
Proposing solutions utilizing proprietary technologies
Q3:What kind of technology and solutions do we offer for our customers’ quality issues?
Yamaguchi:We have developed various solutions by utilizing our core technologies. For powder storage of materials, we keep them in our dedicated cabinets that prevent moisture absorption, thereby enabling long-term storage. We have also developed proprietary equipment that are highly valued by our customers that can perform stable modeling without being affected by the season by reducing oxygen and moisture to the lowest possible levels to suppress seasonal effects during the modeling process. In addition, we have developed a number of unique technologies to improve the quality of welding during modeling. These advancements can significantly contribute to stabilizing the modeling quality, which has been a persisting challenge for us.
Ono:Furthermore, we have established partnerships with the world’s most advanced manufacturers in Europe and the United States. This allows us to offer a comprehensive range of metal 3D printers utilizing nearly all methods and featuring distinctive metal powders to cater to a wide array of needs. Through technical discussions with customers who have manufacturing expertise and actual sample modeling at the AM Innovation Center, we are able to provide one-stop proposals for specific solutions that only we can offer. Due to the distinct characteristics of each method, we have earned a high reputation for proposing the best combination of models, systems and metal materials in terms of both cost and functionality, which is something only we can provide, based on the purpose and application.
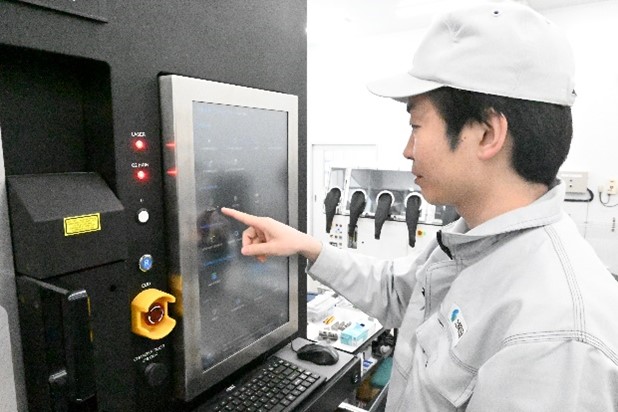
Mr. Ono explaining the equipment (left) and Mr. Yamaguchi at work
Aiming to expand the use of metal 3D printers
Q4:What are your future goals through the development work you are responsible for?
Nanao:In metal 3D printers that use wire as a material, the modeling is performed by accumulating layers of welded wires. We will work on developing technology to automatically optimize this welding path using the latest AI to stabilize the modeling quality and to reduce the modeling time.
Ono:Currently, our main users are large to medium-sized companies, but a single metal 3D printer can serve a variety of purposes. In a “decentralized society” that is expected to prevail in the future, we would like to promote the use of 3D printers at local companies, thereby stimulating the local economy and promoting regional development.
Yamaguchi:We would like to attract potential users from a technical perspective that metal 3D printers can be used for a wide range of applications. As I mentioned earlier, what can be done with 3D printers varies significantly depending on the printer and the materials used. By showcasing the uses possible with each type of printer, we hope to enhance the value proposition for our customers.
Nakanishi:We aim to create an environment that facilitates accessibility for people who have never used a metal 3D printer before. Unlike traditional manufacturing methods, this technology does not necessitate specific gender or prior experience. In addition, we believe that by using it, people will be prompted to ask themselves, “Can it do this?” or “Can we use it for something like this?” Thus, creating new ideas. We would like to take such needs into account and actively promote the widespread adoption of metal 3D printers.
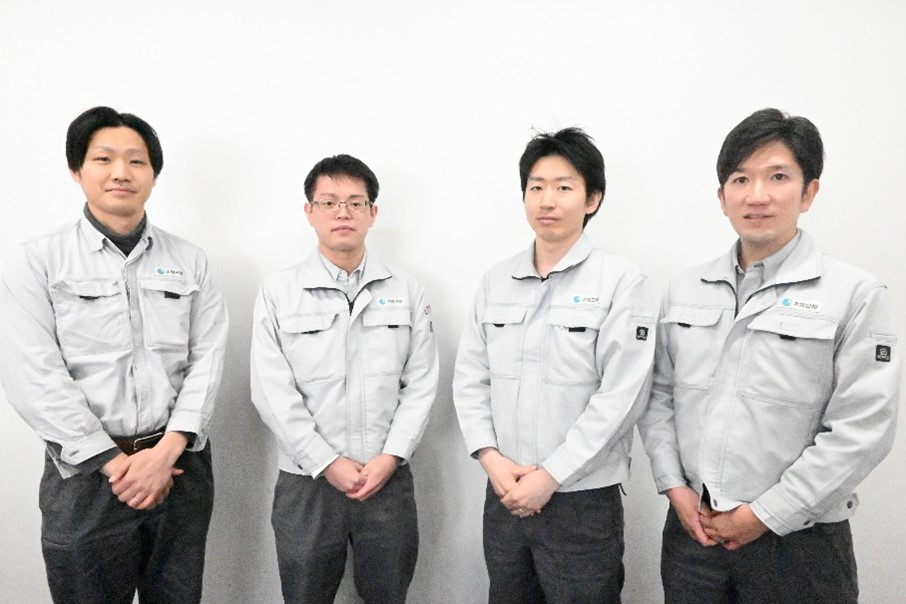
The interviewees: Mr. Nanao, Mr. Nakanishi, Mr. Yamaguchi and Mr. Ono, from left to right